Design Process
Research Phase
Market Needs: 1,2-dichloroethane (DCE) is heavily produced in the U.S. for vinyl. Since it is highly volatile, the workers who work in vinyl production are at high risk of breathing in the toxic chemical. In addition, the environment and water sources are at high risk of contamination. To prevent the DCE from entering into the human body and into the environment, the use of a biofiltration system is used to convert 1,2-dichloroethane in the air into less harmful products (glycolate).
Biofiltration: When exploring different possibilities, we focused on looking for a filtration method that is sustainable and environmental friendly. We decided to look into biofiltration–a biological air treatment that’s commonly use in industries. Biofiltration uses minimal amount of energy since the air is filtered by passive diffusion, and the medium used in biofiltration is decomposable.
Xanthobacter autotrophicus: Xanthobacter autotrophicus was chosen as a candidate of interest since it possesses the ability to carry out a series of reactions that can convert 1,2-dichloroethane into glycolate. First, dichloroethane is converted to chloroethanol, which is then converted to chloroaldehyde. Next, chloroaldehyde is converted to chloroacetic acid. Finally, chloroacetic acid is converted to the end product, glycolate, which is a very unreactive and low health hazard compound.

Prototyping
Detailed scientific procedures can be found here
Growing Xanthobacter autotrophicus: In order to grow the bacteria strain of interest, special nutrient agar was made from DI water, beef extract, peptone, and agar. The nutrient agar was autoclaved to sterilize it to get rid of any bacteria that may interfere with the growth of the target bacteria strain. In addition, a flame was set up before the agar was poured into the petri dishes to make the environment as sterile as possible.
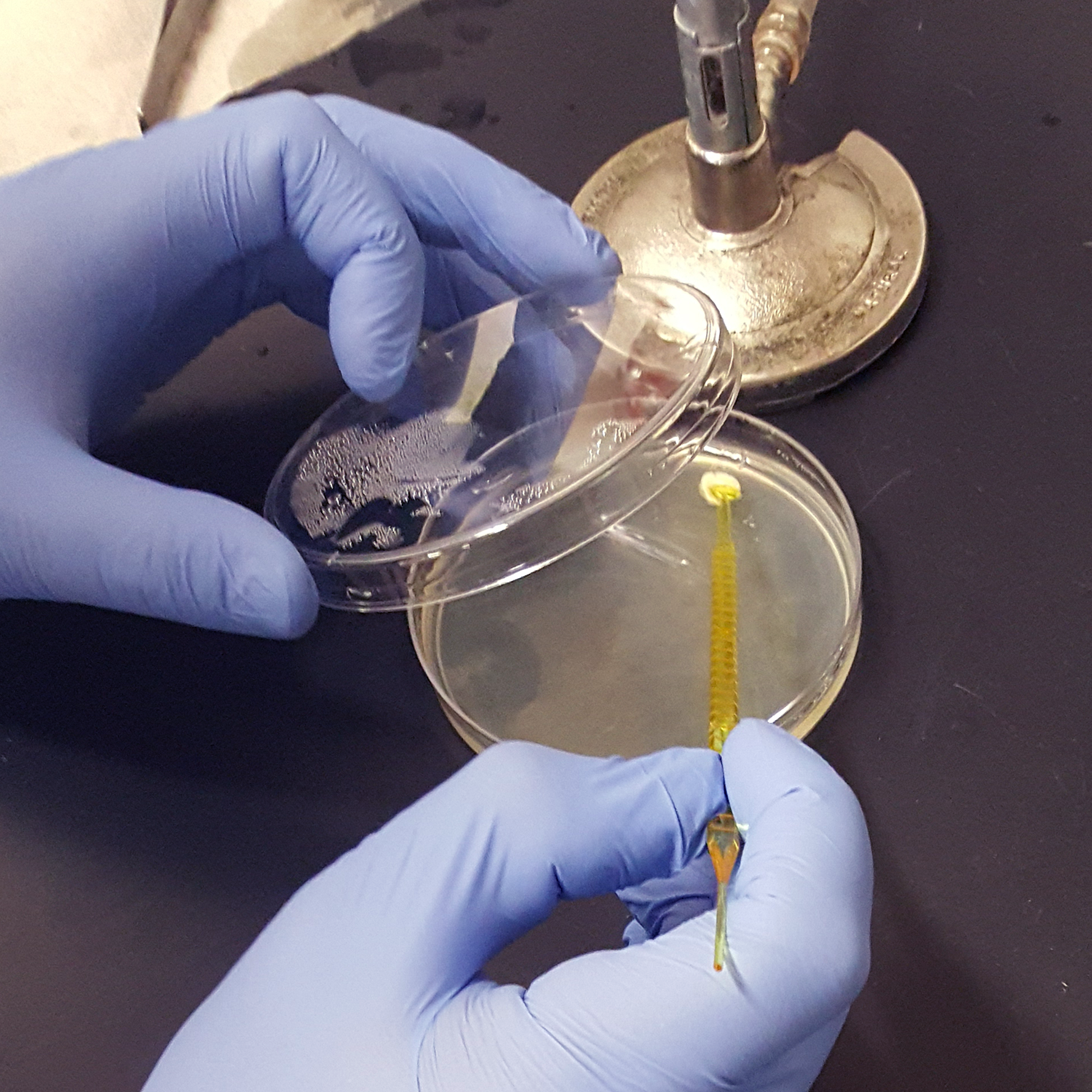
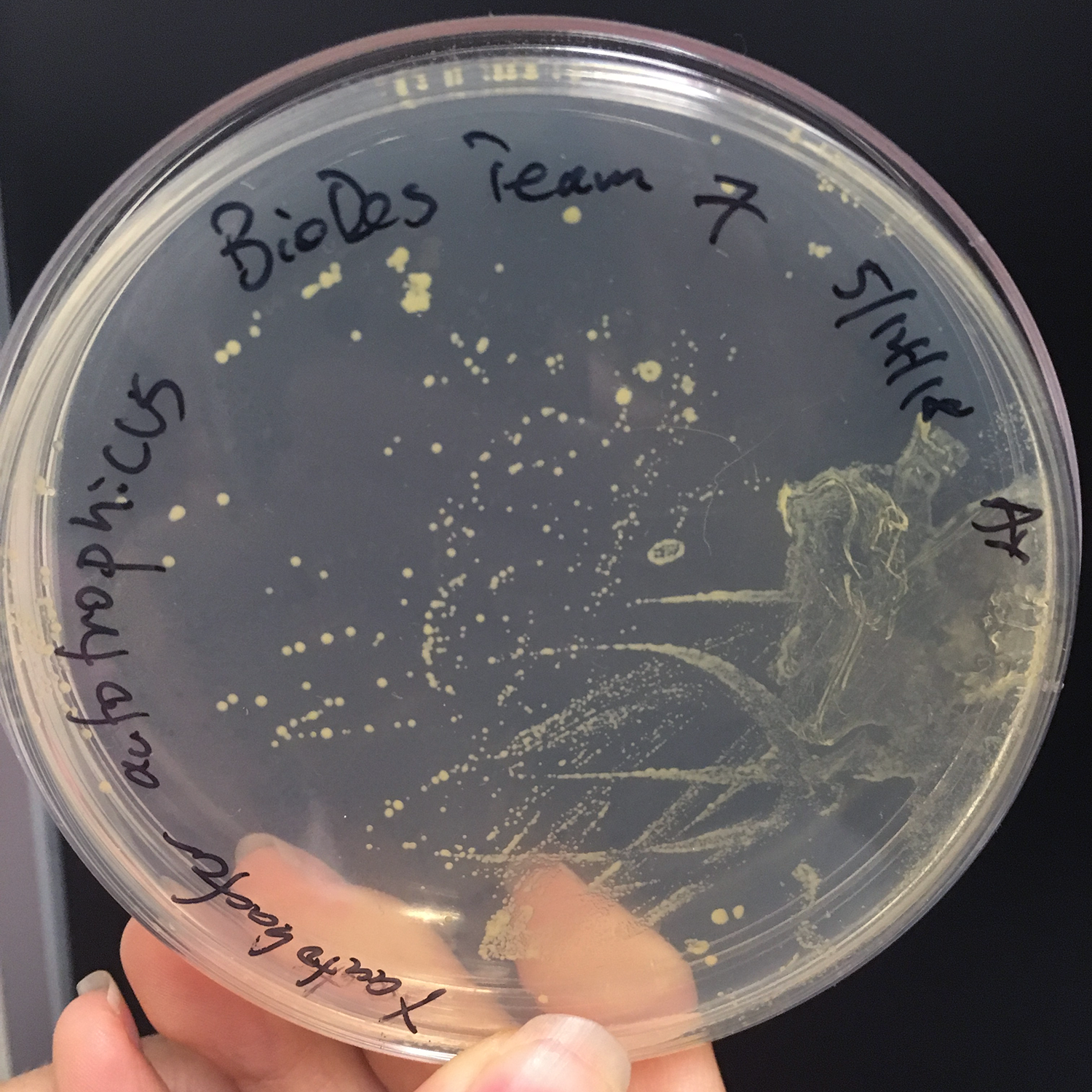
After colonies of Xanthobacter autotrophicus were grown, one colony was added to liquid media (composed of beef extract and peptone) and grown in a shaking incubator. This was used in in the expirement below titled "Integrating Xanthobacter autotrophicus with the Pellicle."
Growing Cellulose in Citrus: To experiment growing bacteria cellulose using a more sustainable media, we worked with another group of students to grow bacterial cellulose in citrus juice. After citrus waste was collected from the residential area in Davis, it was sliced and juiced. Ethanol, acetic acid, and sugar were added to the citrus juice, which was then distributed in three plastic containers. Some existing kombucha tea and a piece of a pellicle was then added to the mixture to seed it. The SCOBY was left to grow for 2 weeks at room temperature.
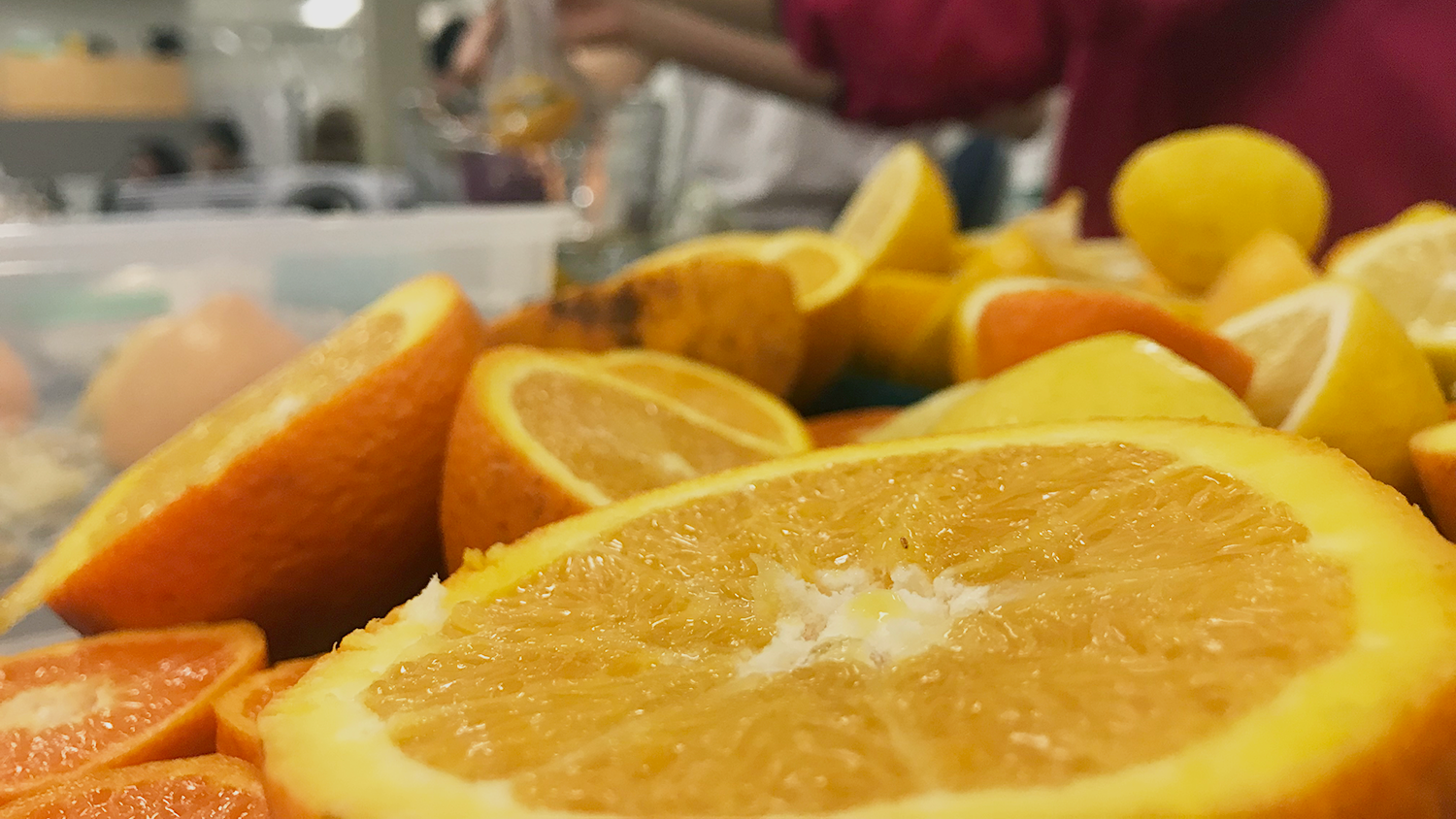
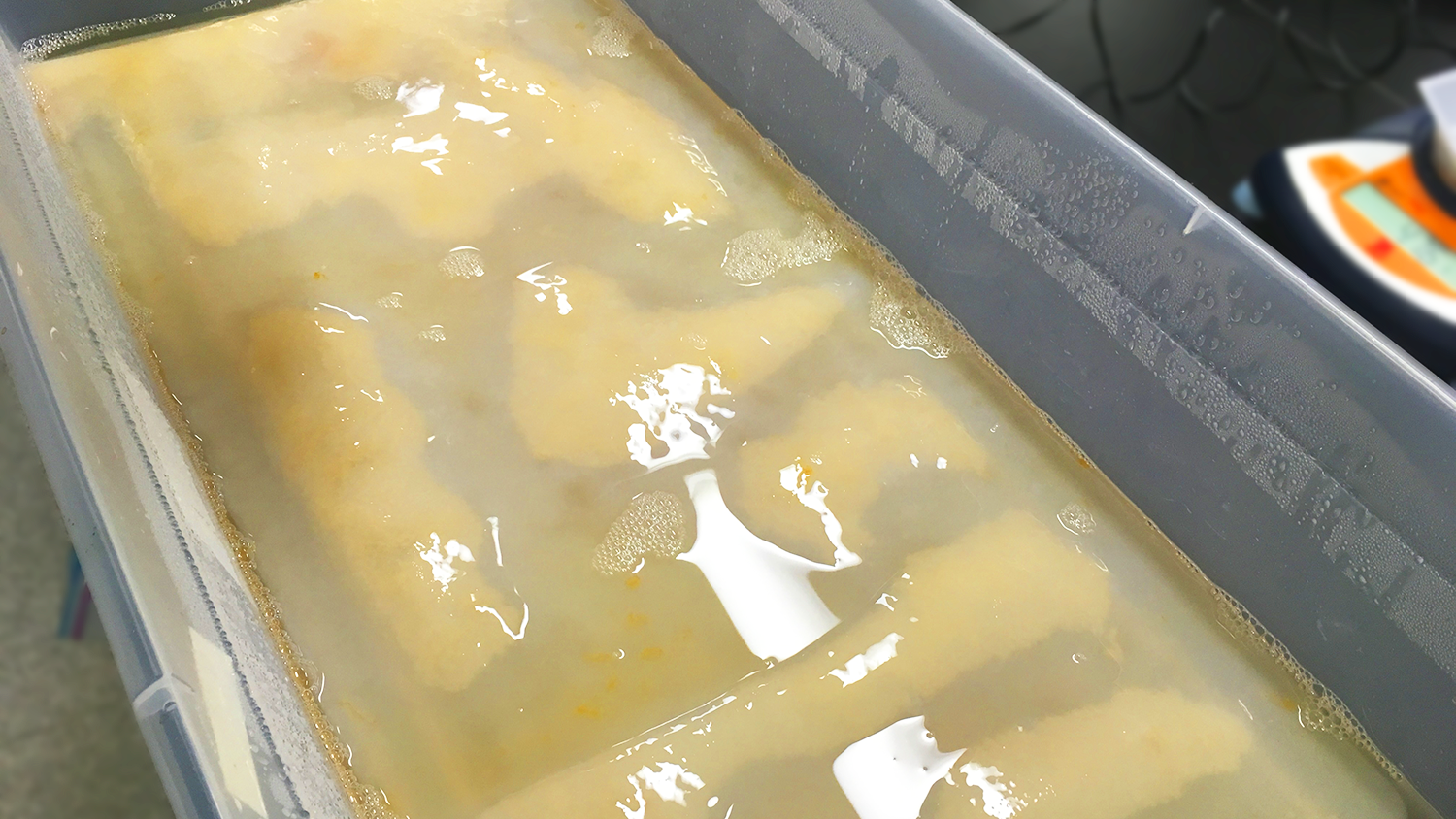
The pellicle in citrus media was growing at a higher rate than ordinary kombucha media. We removed one of the pellicle after a week of waiting. The pellicle was almost fully grown, with numerous small bumps on the surface. The pellicle growing in citrus media was then removed from the media and left to dry in a room temperature environment. Compared to the dried bacterial cellulose we collected previously, the dried citrus pellicle was softer and more flexible.
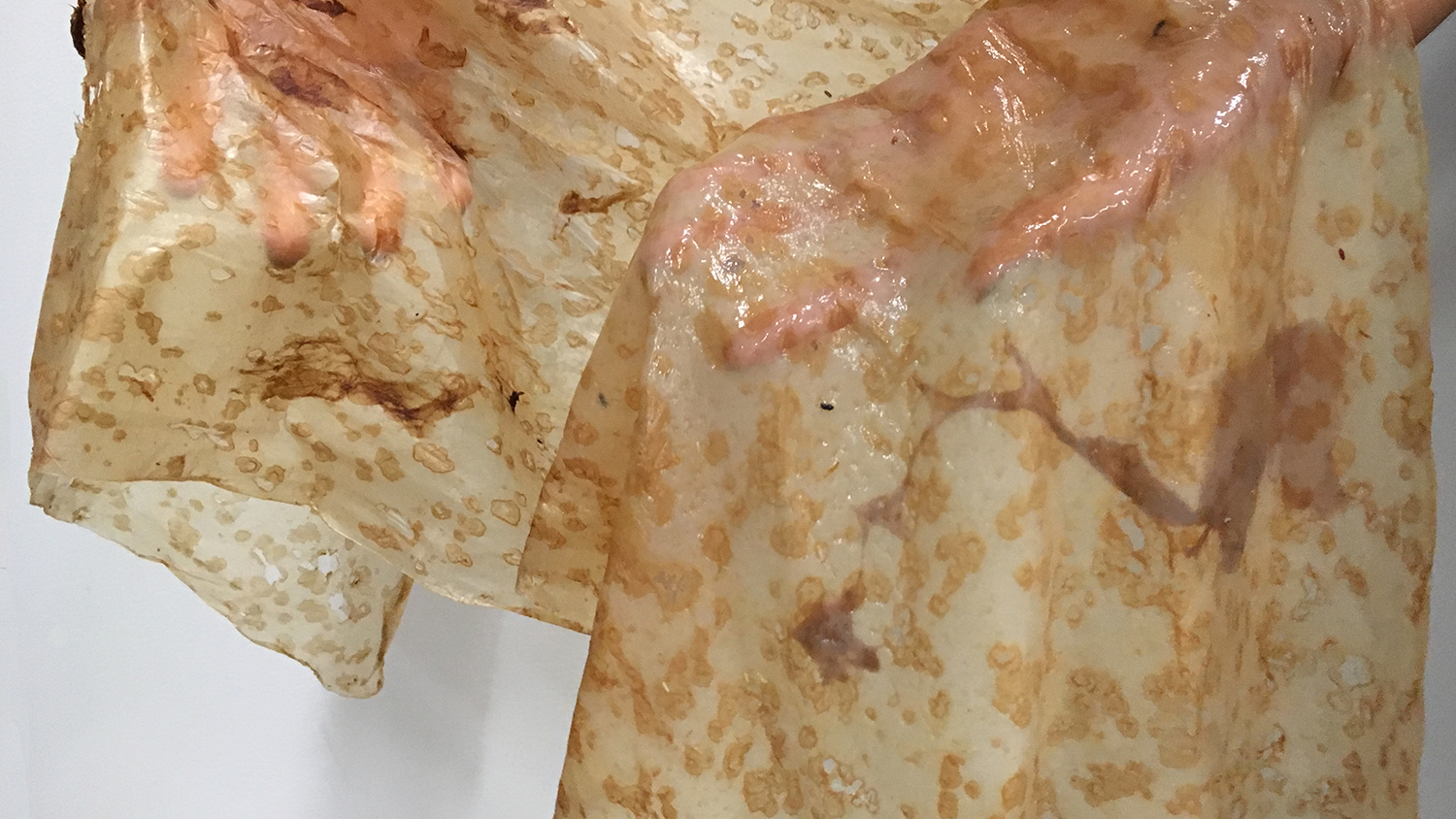
Purifying Cellulose: The fresh grown kombucha medium naturally emits an unpleasant smell. To eliminate the smell of the SCOBY, we obtained pellicles that had been pre-soaked in NaOH. At this point, the smell was partially eliminated. To neutralize the pellicle, we soaked it in water before being soaked in an acidic bath of 5M hydrochloric acid. After the acid bath, the pellicle was then rinsed in deionized water and soaked for 24 hours. Few drops of NaOH was added into the water bath to reach a pH of 7. The pellicle was left to sit for 24 hours before it was removed from the bath, lightly rinsed, and left to dry in a room temperature environment. While drying, the pellicle was massaged once per day.
After the pellicle was neutralized and dried, the pure cellulose showed a pure white color with the texture of thin layers of plastic. The odor is completely eliminated; the washed pellicle is now odorless and colorless.
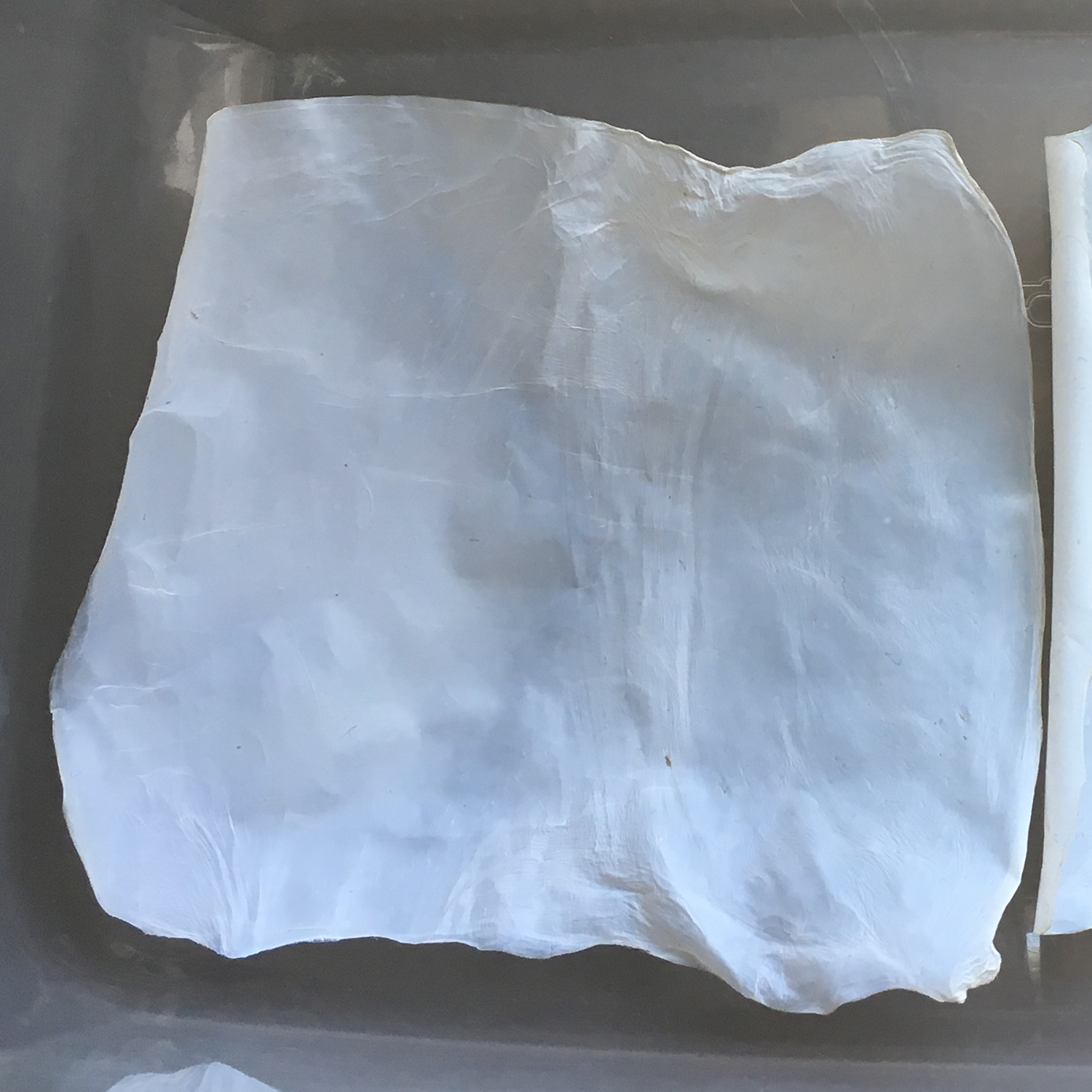
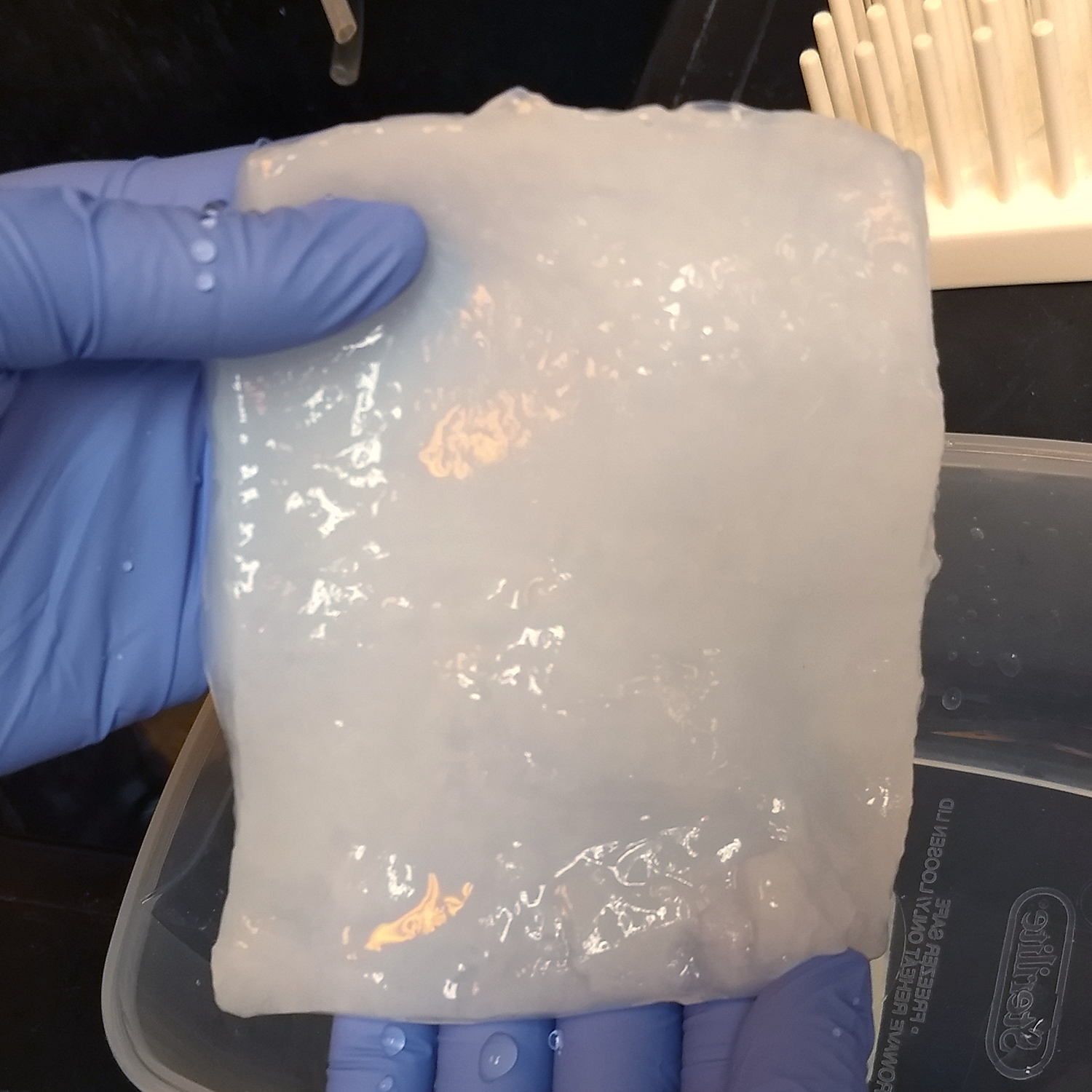
Integrating Xanthobacter autotrophicus with the Pellicle: [in progress]
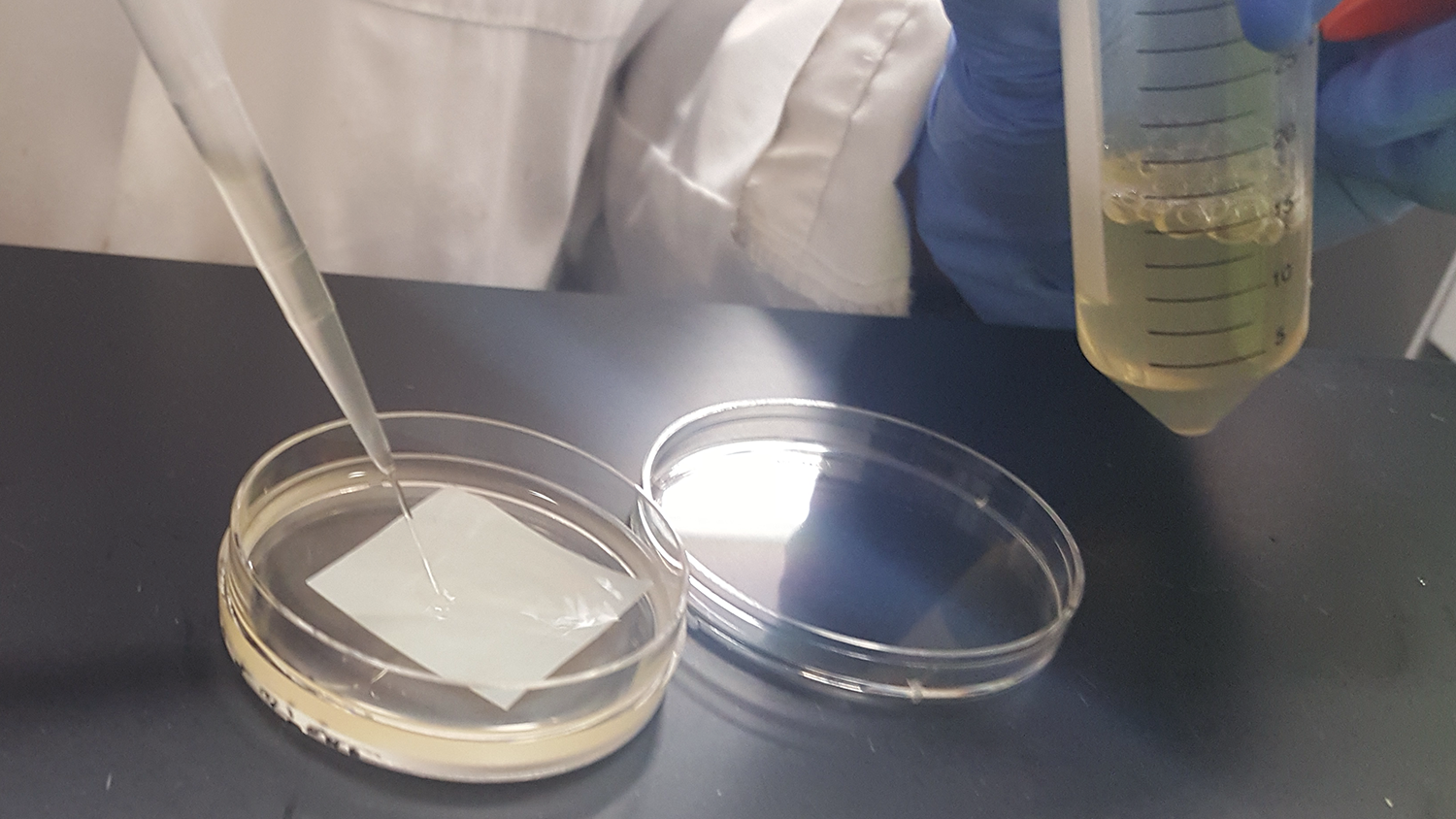
We tested two different integration methods: vacuuming then soaking and soaking. 3 samples and one control for each method were tested. [Results in progress]
After the 8 samples described above were soaked for 4 days, DNA samples were extracted. 1 control extraction was taken from the original liquid media/bacteria mixture. PCR analysis was run on both the samples and the control, and DNA amplification was checked using Gel electrophoresis.[Results in progress]
[metabolic activity in progress]
Panel Prototyping: After we obtained the pellicle, we stretched it on an embroidery hoop that has a diameter of 8 ¾ inches. The pellicle is then placed on a flat surface and left to dry at room temperature. The wet pellicle dried within 5 hours, resulting in a layer that was relatively thin and smooth in comparison to the pellicles that were laid on a flat surface to dry. Blue food dye was applied to the dried pellicle. After the applied dye dried, a small amount of pressure was applied, which broke the pellicle. It did not pass the pressure test.
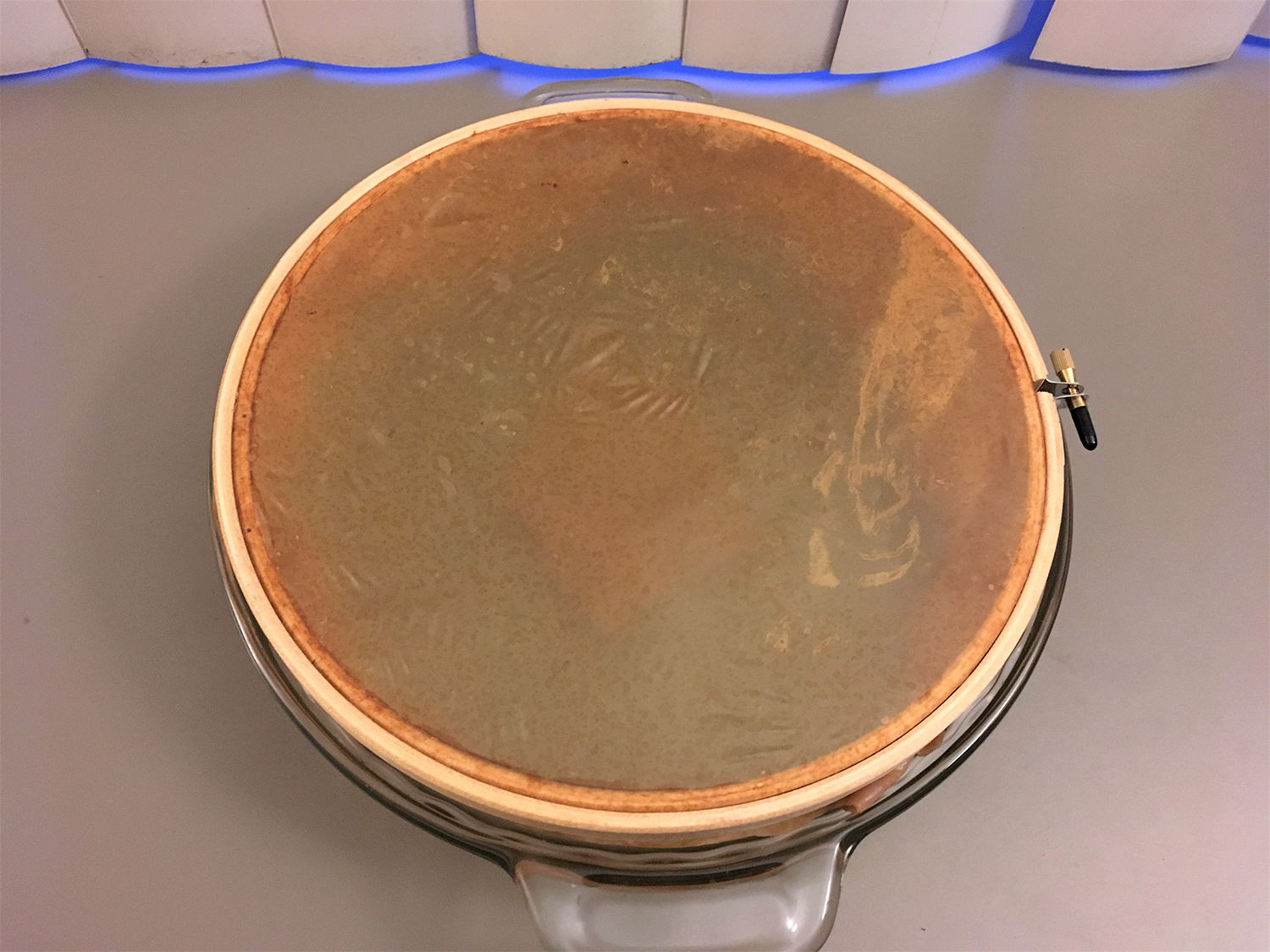
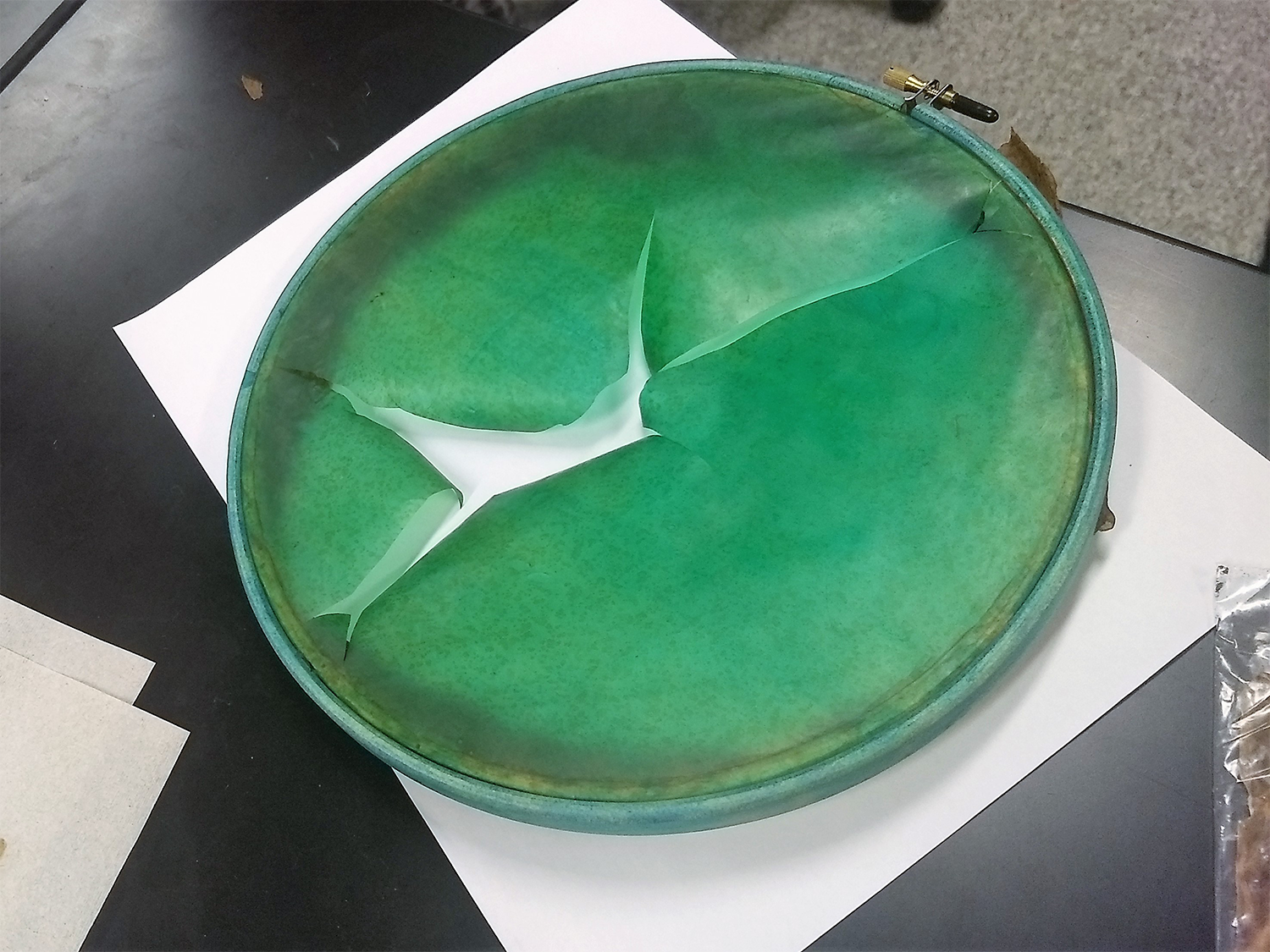
Final Product
Final Panel Prototype: These to scale models of the BacterFilter panel display the quality of the bacterial cellulose when it is dyed and stretched over the panel frame. Shown is just one option for color and shape combination that is possible. The panel fabric was dyed with food-grade blue dye after being rinses repeatedly to wash away any remaining bacteria/yeast.
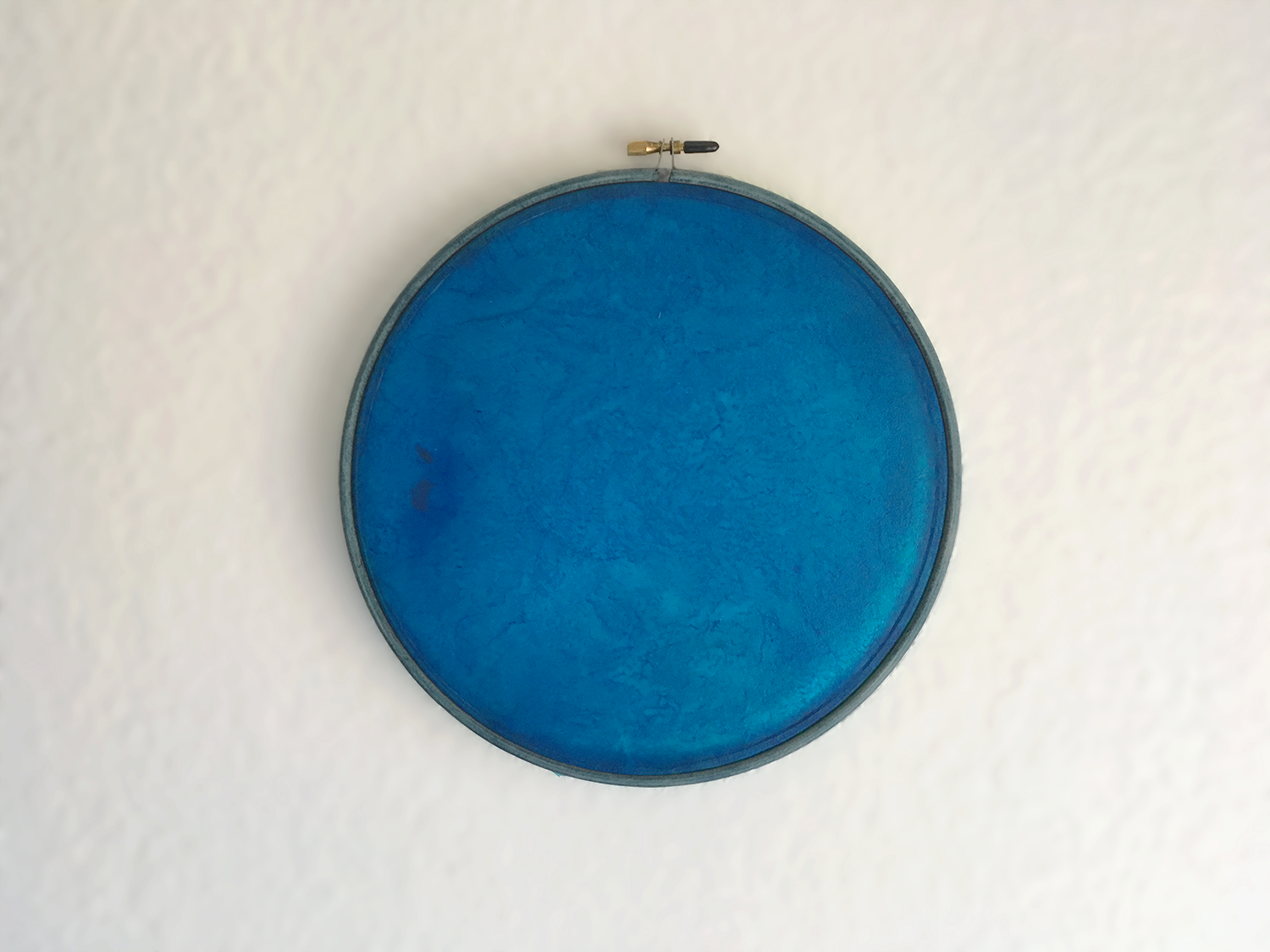
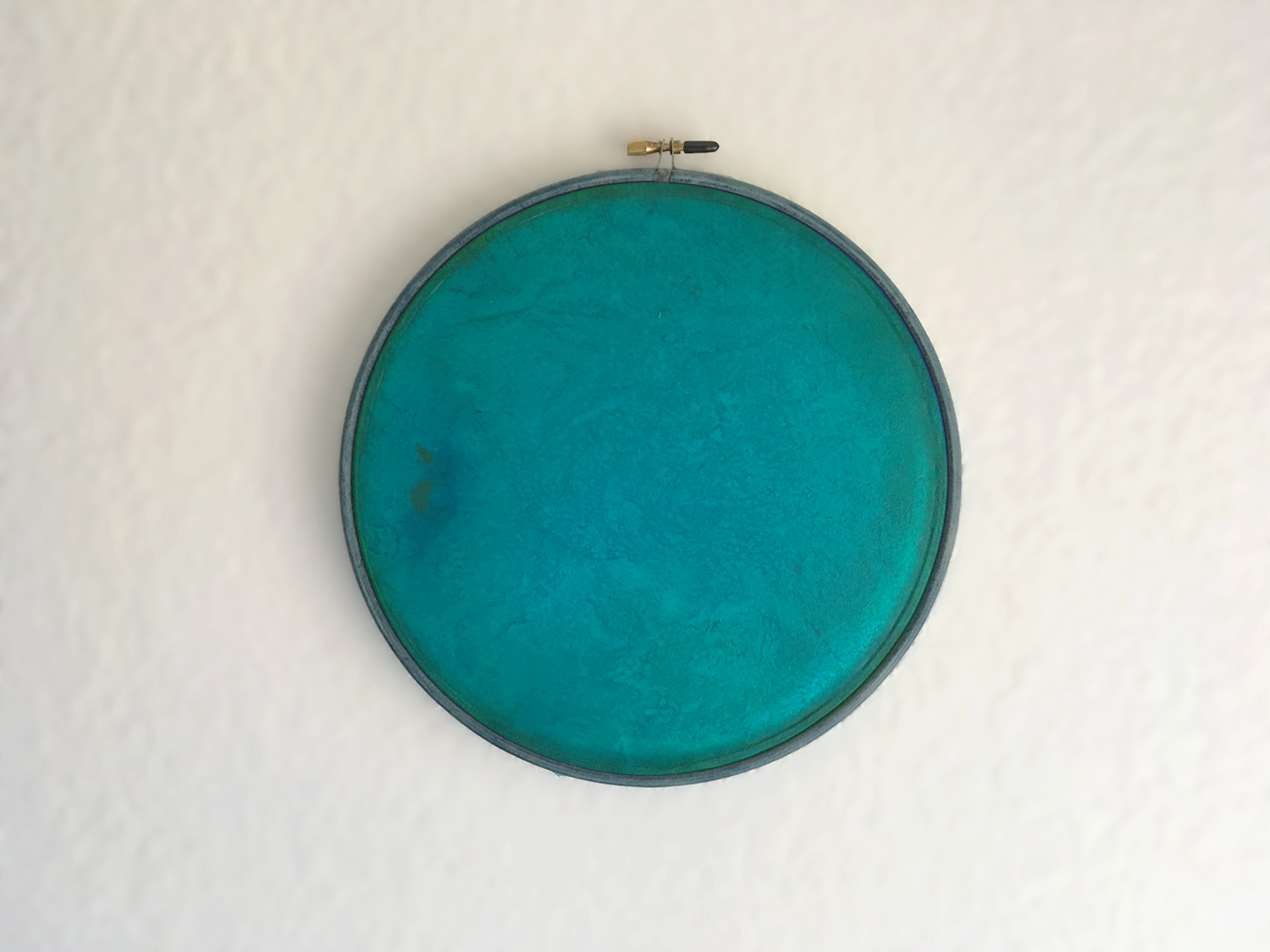
Final Scale Model Prototype: The study model at the left, built at a 1/2" = 1' scale, and the digital rendering to the right show how BacterFilter panels interact with and affect the target environment.

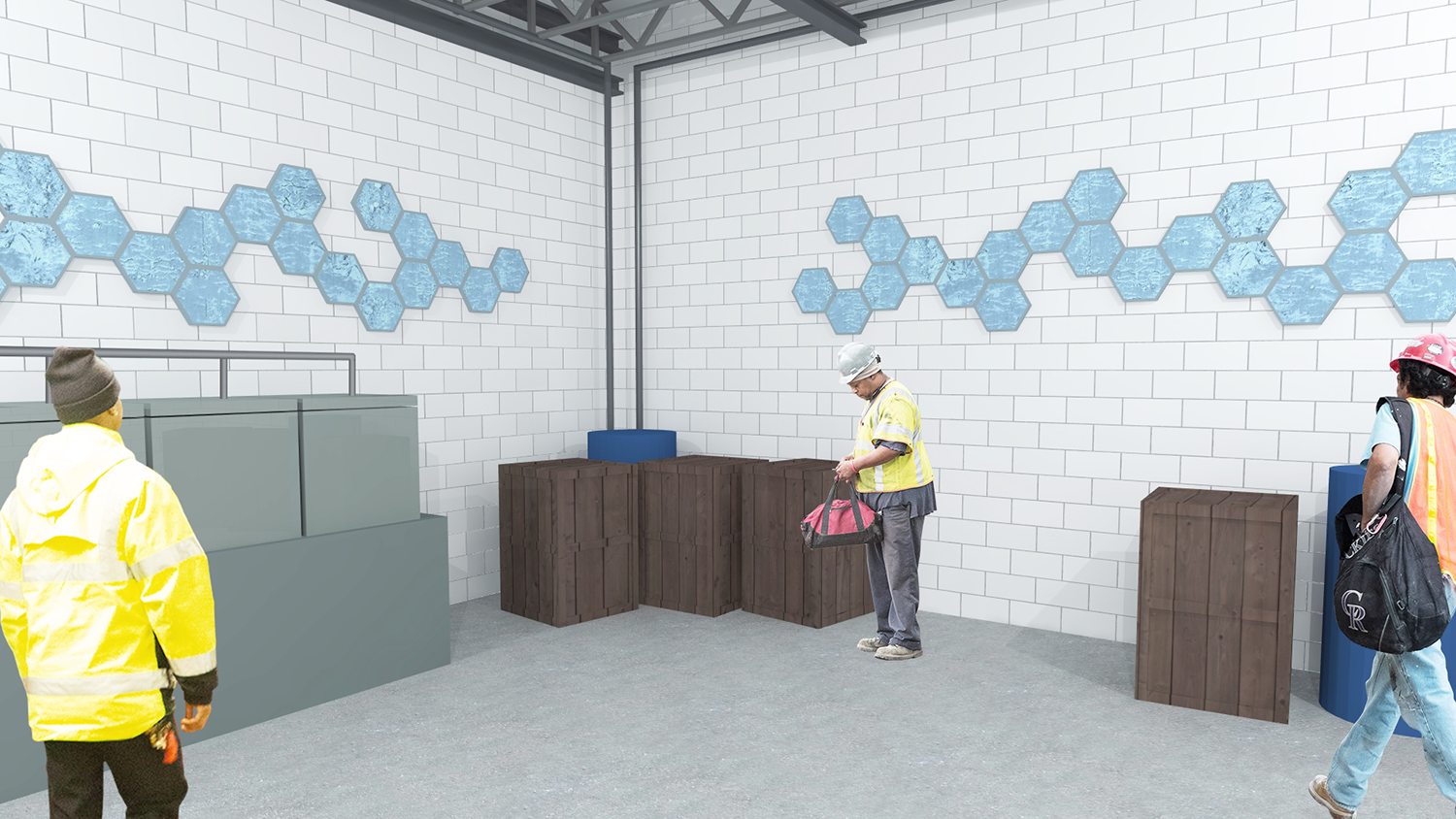